The control of pressure during the embossing manufacturing process of SPC flooring film has a significant impact on the finished product's quality, appearance, and performance. The level of pressure applied can affect several aspects of the final product:
1. Embossing Depth and Clarity: The pressure controls the depth of the embossed pattern or texture on the wear layer of the SPC flooring film. Higher pressure typically results in deeper and more defined embossing, while lower pressure can produce shallower textures. Inconsistent pressure can lead to uneven patterns.
2. Realism and Aesthetics: The level of pressure influences how closely the embossed texture replicates the look and feel of natural materials like wood or stone. Accurate embossing is crucial for achieving a realistic and aesthetically pleasing appearance.
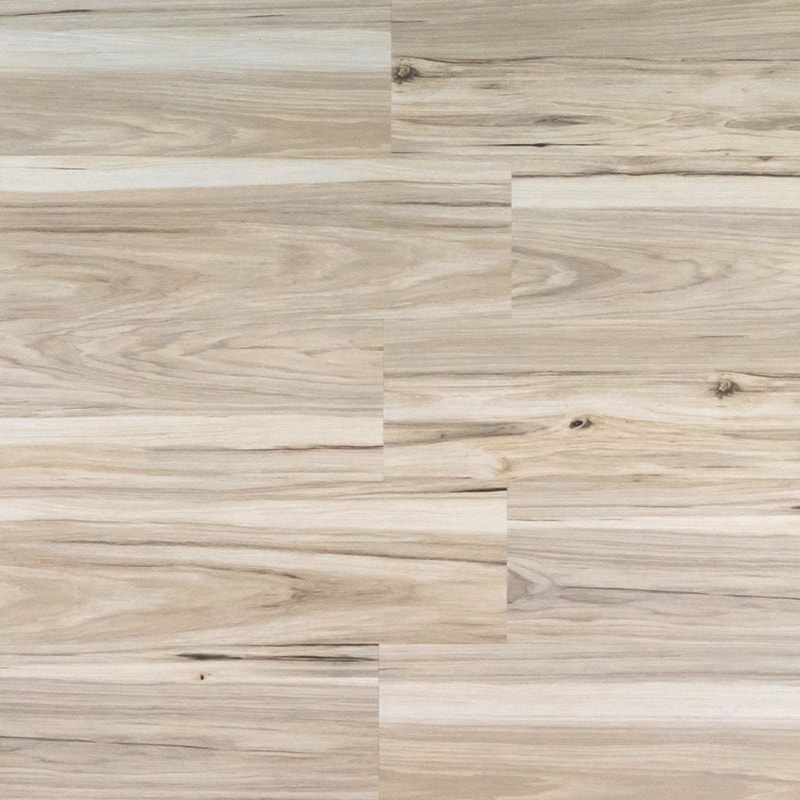
3. Tactile Feel: The tactile feel of the SPC flooring is determined by the depth and texture of the embossing. Proper pressure control ensures that the surface feels convincing to the touch and closely resembles the natural material it imitates.
4. Resistance to Damage: The correct pressure setting helps prevent damage to the film, such as stretching, tearing, or deformation. It also contributes to the film's ability to withstand normal wear and tear.
5. Adhesion to Core Layer: Proper pressure control ensures that the embossed wear layer adheres securely to the SPC core layer during the manufacturing process. Weak adhesion could lead to delamination or separation of layers, impacting the product's structural integrity.
6. Production Efficiency: Optimizing pressure control can enhance production efficiency by minimizing the need for rework or adjustments. It helps ensure a smooth and consistent embossing process.
7. Waste Reduction: Accurate pressure control can minimize material waste by reducing the likelihood of producing defective or substandard rolls of flooring film.
8. Material and Energy Efficiency: Maintaining the right pressure levels contributes to efficient material and energy use during the manufacturing process, potentially reducing production costs.
In summary, the pressure control during SPC flooring film embossing is crucial for achieving the desired texture, realism, durability, and consistency of the finished product. Manufacturers must carefully set and maintain the appropriate pressure to ensure the highest quality and performance of SPC flooring films that meet market and customer expectations.