Corner film, also known as edge protection film or corner guard film, is used to protect the corners and edges of various products during transportation, storage, or handling. The production steps for corner film may vary depending on the specific manufacturing process and equipment used. However, here is a general outline of the production steps:
Material Preparation: The production of corner film starts with the preparation of the raw materials. The main material used is typically a flexible plastic film, such as polyethylene (PE) or polypropylene (PP), which is sourced in rolls or sheets. The material may be pre-colored or require additional coloring during the production process.
Extrusion or Coating: The plastic film is fed into an extrusion or coating machine. In the extrusion process, the plastic material is melted and forced through a die to form a continuous film. In the coating process, the plastic film is coated with a layer of molten plastic material. This step helps provide the desired thickness and strength to the corner film.
Cooling and Solidification: After extrusion or coating, the film passes through a cooling system, such as cooling rollers or a water bath, to solidify the molten plastic and stabilize its shape and dimensions.
Printing (Optional): If required, the corner film may undergo a printing process to add labels, logos, or product information. This step is typically performed using a flexographic or screen printing machine.
Slitting and Cutting: The solidified film is then slit and cut into narrow strips or sheets of the desired width, corresponding to the width of the corner film. The slitting process may involve specialized slitting machines that ensure precise dimensions and smooth edges.
Folding and Forming: The strips or sheets of corner film are folded or formed into the desired shape, typically a right angle or U-shape, resembling the corner or edge of the product it will protect. This step may be performed using automated folding machines or manually with the assistance of fixtures or molds.
Inspection and Quality Control: Throughout the production process, quality control checks are conducted to ensure that the corner film meets the required specifications. This may include visual inspections for defects, measurements of dimensions and thickness, and testing for strength and durability.
Packaging and Distribution: Once the corner film passes the quality control checks, it is packaged into rolls, stacks, or bundles for storage and distribution. Packaging materials such as plastic bags, boxes, or shrink wrap may be used to protect the corner film during transportation.
It's important to note that the specific production steps and equipment used can vary between manufacturers. Advanced production processes may incorporate additional steps, such as surface treatment for improved adhesion, embossing for texture or branding, or the inclusion of additional layers for added strength or cushioning.Besides,The chemical composition of corner film, which is typically made of flexible plastic materials, can vary depending on the specific type of film and manufacturer. The most common materials used for corner film production are polyethylene (PE) and polypropylene (PP). These materials have different chemical structures and properties. Here's a brief overview of their chemical compositions:
Polyethylene (PE):
Polyethylene is a thermoplastic polymer that is widely used in the production of various plastic films, including corner film. The chemical composition of polyethylene consists mainly of carbon and hydrogen atoms. It is a polymerized form of ethylene monomer. The basic chemical formula for polyethylene is (CH2)n, where n represents the number of repeating units in the polymer chain. Depending on the density and molecular weight, different types of polyethylene can be produced, such as low-density polyethylene (LDPE), linear low-density polyethylene (LLDPE), and high-density polyethylene (HDPE).
Polypropylene (PP):
Polypropylene is another thermoplastic polymer commonly used in corner film production. It is a polymerized form of propylene monomer. The chemical composition of polypropylene consists mainly of carbon and hydrogen atoms. The basic chemical formula for polypropylene is (C3H6)n, where n represents the number of repeating units in the polymer chain. Polypropylene exhibits excellent mechanical properties, chemical resistance, and heat resistance, making it suitable for various applications.
In addition to PE and PP, corner film may contain additives, fillers, or colorants to enhance specific properties or meet certain requirements. These additives can include stabilizers, antioxidants, UV absorbers, slip agents, antiblock agents, or processing aids. The specific combination and concentration of additives may vary depending on the desired properties of the corner film.
It's important to note that the exact chemical composition of corner film can vary between manufacturers and specific product formulations. If you have a specific corner film product in mind, it's recommended to refer to the manufacturer's technical datasheets or contact the manufacturer directly for detailed information on the chemical composition of their specific product.
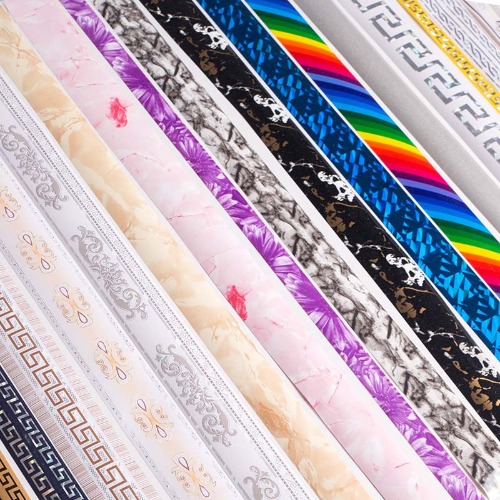
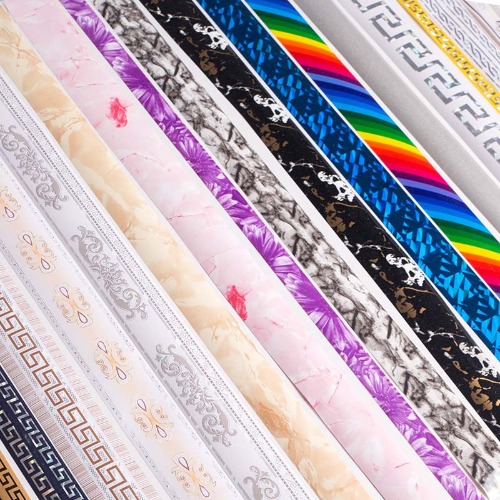